The formal test activities consist of functional testing, bench testing, fault insertion testing and Design Verification and Production Verification (DV & PV) testing.
Functional
Dana creates functional tests for each ECU product. Functional tests often begin as a manual exercise in the prototype phases of a program and mature into full automation to support DV & PV efforts. The functional test provides functional verification through the ECU’s vehicle level interconnect. Employing a pin-by-pin approach where the functionality associated with each pin is verified using external loads, excitation source and multi-meter measurements.
Bench
Bench testing is a manually intensive, thorough functional requirements-based design verification step. Dana typically performs bench testing on early hardware samples to provide verification that the hardware design satisfies requirements. Later product engineering steps will typically have automated functional test capabilities that will supersede these early manual tests.
Detailed hardware design implementations are also verified during bench testing. Testing the design implementation details provides insight into a product’s suitability for intended environment and operative life. Some design implementation details include internal power supply voltage rail performance (voltage accuracy, voltage tolerance, load regulation, ripple voltage, current capability, efficiency), analog to digital converter performance (resolution, linearity, dynamic range, accuracy, signal-to-noise ratio), clock quality (skew, jitter, ringing), and signal integrity (cross-talk, reflection, overshoot, damping). These types of design implementation bench tests offer real-world verification of the theoretical worst-case analysis results.
To provide confidence, initial testing is done at nominal operating conditions for temperature and supply voltage. Robustness of design is verified by repeating critical tests at the operative temperature and supply voltage extremes. Critical functions include internal power supplies, communication buses, power-up and thermal management.
Design Verification Plan
The Design Verification Plan (DVP) covers the full scope of the design verification testing for the ECU being designed. This includes mechanical, electromagnetic immunity, electromagnetic emissions, sealing, mechanical shock, vibration, short circuit, supply voltage disturbances, humidity, and thermal stress. The DV Plan can be extended to include system level and vehicle level components with test responsibilities shared between Dana and the customer.
The Design Verification Plan & Report (DVP&R) is a key testing document tailored to the needs of each customer and their application. Dana starts with a standard suite of test for automotive electronics and tailors the test to meet the specific needs of the customer and there intended application. Light duty passenger cars, heavy duty trucks, and military applications are all part of Dana’s experience with DVP&R.
The authoring of the DVP&R as well as the execution of the DVP are inherent to the Dana engineering process.
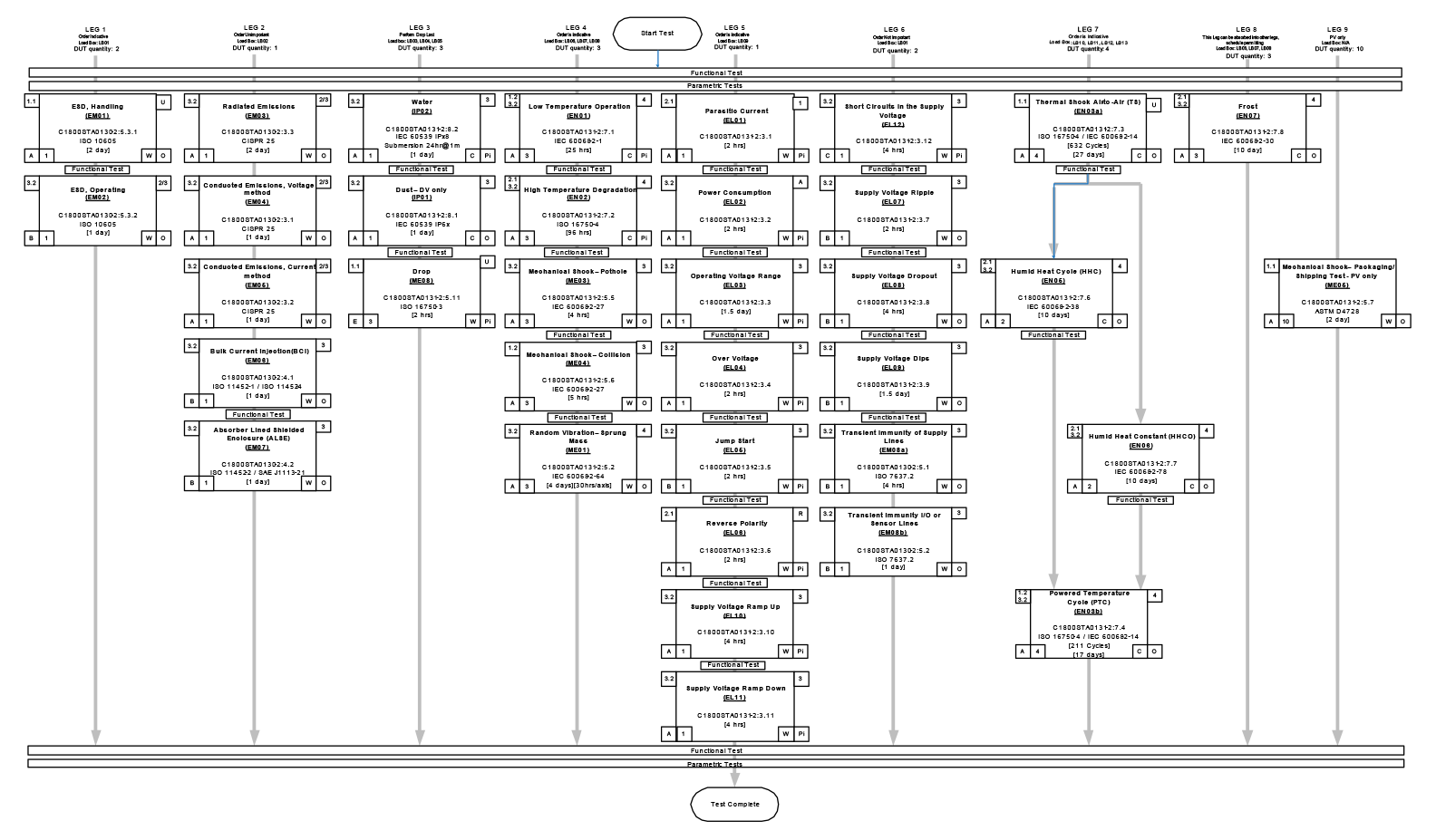